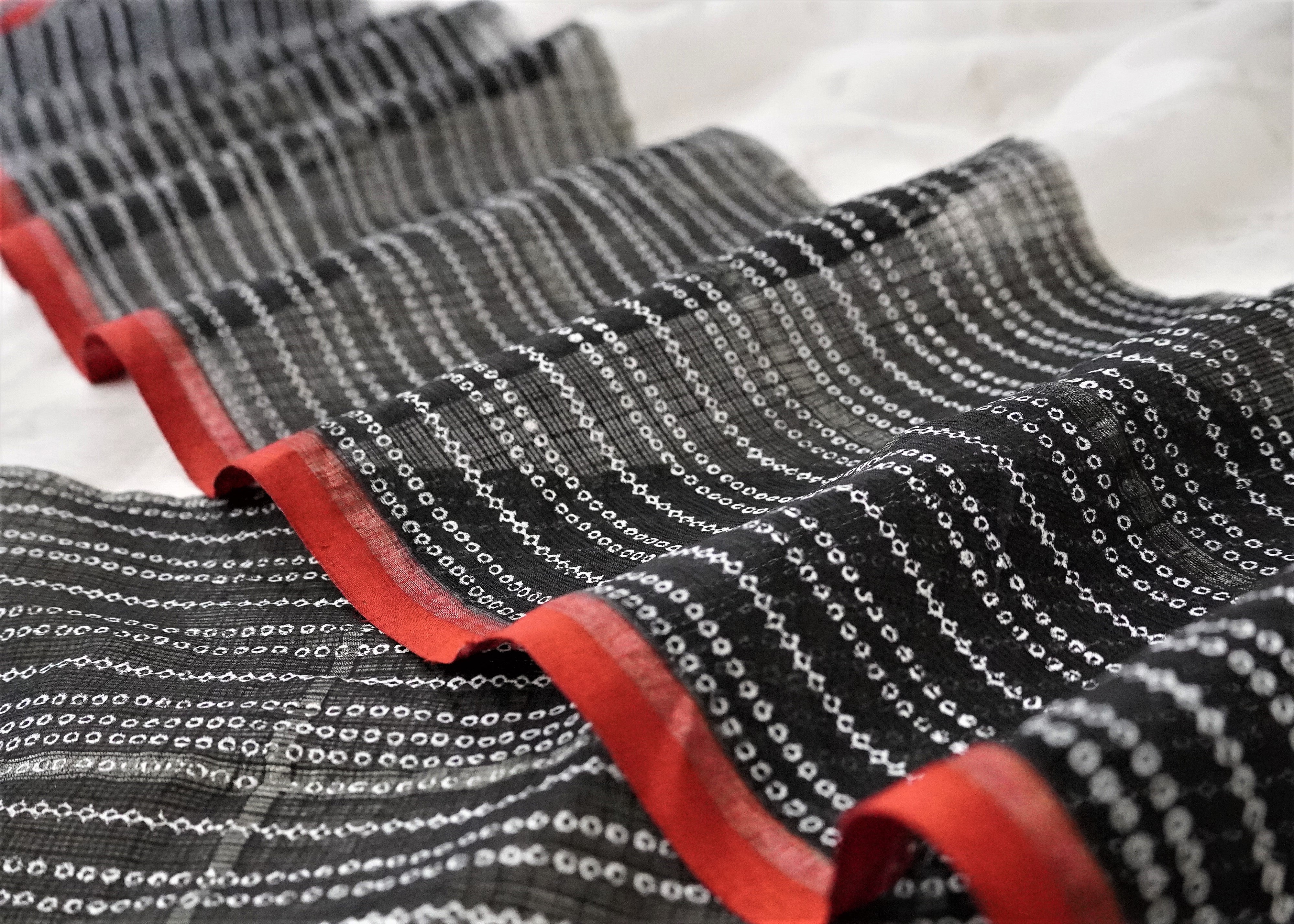
Dvijavanti
How craft evolves and changes with time is a subject that fascinates us. A few months ago, we had the privilege of visiting Kota and had the chance to witness kota weaving process first hand. The power of seeing and understanding craft is something no book or visual aid can come close to.

The rise & fall of kota masuria is a rather interesting to hear from the weavers themselves. A lot is spoken about how weavers from Mysore state were brought over to weave diaphanous gilded garments for the royalty. Fine zari kota is one of the few clusters that still uses a high zari purity till date. The cotton threads are processed locally with starchy paste made from wild onions, sized & warped. The yarn is dyed if required in colours and woven with zari on jaala looms. Till twenty years back, men from the families wove zari kotas but when the demand for kotas receded, the men shifted to other work like construction & factory jobs. In the last few years, demand for Zari Kotas has been steadily growing and this time around it is the women folk who manage the entire supply chain. Patient and meticulous, these women weave the most complicated of patterns by merely gazing at graph sheets. Ms Misbah & Ms Regina Bano from Mr Sharif Ansari’s team work on Parvai commission orders and we appreciate how clean and meticulous their work is.

Dvijavanti was a special commission by a Patron who loves kotas. A special design was created for this project at Kota and the checked saris were woven in pure zari. The pallu features an interesting negative space design motif. The sari itself is a remake of an old sari design from the archives but these designs have not been in vogue for a while.

Our next step with this project was visiting Sanganer & meeting another artist par excellence, Ms Premalatha Sethi. When we explained the project we had for her, she was game for it but the blocks had to be carved to mimic the original block. We also wanted to test how prints would affect the saree fabric so a few tests were performed and the project began to take shape.
Unlike Kota, Sanganer’s popularity has only grown. From simple bed covers to kurtas, special orders for design houses to export orders, the industry has more than thrived. The industry provides employment opportunities to almost everyone that enters it. There is a space for nuanced work as well as mass production and the industry is competitive & male dominated.
While the weaver women of Kota find themselves being the custodians of a dying weave, Ms Sethi has the formidable job of finding her voice in a male-dominated industry. It is beautiful to note the prints have evolved with time. There was a time when all cloth was printed in Syahi Begar (black & red) with motifs inspired by everyday life. Today western inspired minimalist designs dominate the market in pastel pinks, peaches, turquoise & greens - colours that never existed in the vocabulary. Likewise in Kota, the original designs have been replaced by motifs & designs from Paithan, Benaras & Kanchipuram. The weavers weave designs that are sported by celebrities and the biggest market for Kotas is in fact, Telengana & Andra.
Dvijavanti marries two beautiful art forms and true to her name, this has been birthed twice - once in Kota and once more in Sanganer.
The original saree had a white body with a black border and selvage but we also made a few variants in the same colour scheme. Every sari is available as a single piece only.
A few things to note about this project:
- While Jaala looms are dying everywhere in the country, rapidly replaced by jacquards or even mechanised looms, some of the most complicated loom arrangements are done easily in Kota. Since Kota is so far & remote, technology & mechanisation hasn’t reached them yet.
- Block prints are common enough but investing in new blocks led by design is something that is still new to us and our artists and we are quite enjoying this journey in Sanganer
- We love working on commissioned work are they are mindful & caters to the patron’s wish. But we also realise how this process allows the patron to inch closer to the craft process, understand the nuances better and in the process appreciate the end result more.
About the author: Priyanka is a sari lover & deeply passionate about weaves. She combines her love for writing & weaves by developing original content for Parvai. The opinions expressed in this article are Parvai's. Copyright laws bind this content.
Leave a comment
This site is protected by hCaptcha and the hCaptcha Privacy Policy and Terms of Service apply.